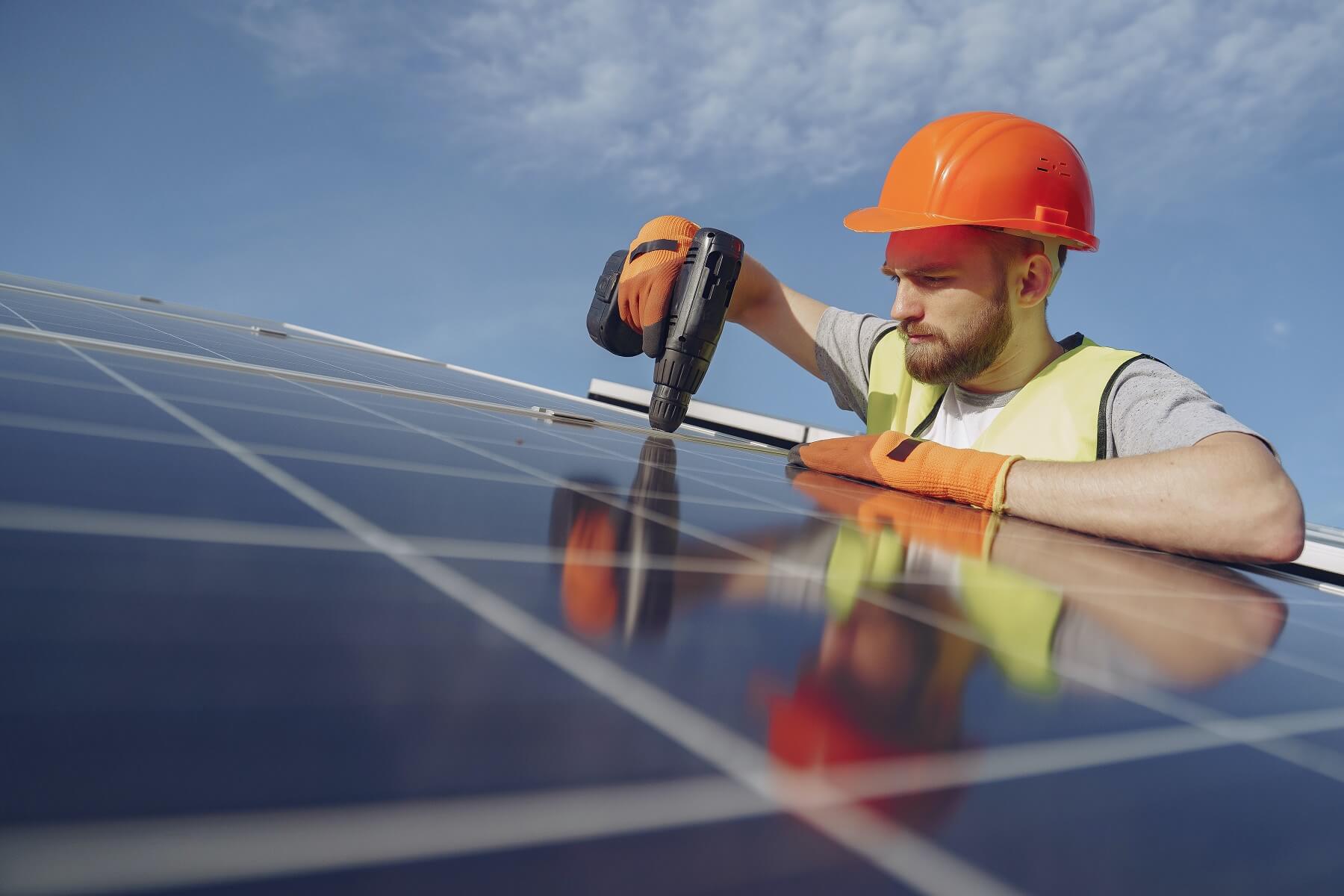
ISO 45001 Occupational Health and Safety Management System
This standard is designed to greatly assist organisations of any size in creating and maintaining a safe working environment for their employees.
About ISO 45001 OH&S Management System
ISO 45001 is the newest Occupational Health and Safety Management System standard and is aligned with both ISO 9001 (Quality Management) and ISO 14001 (Environment Management), and has replaced OHSAS 18001 and AS/NZS 4801.
The framework upon which the standard is built is designed to help organizations create a safe and healthy work environment, prevent workplace injuries and illnesses, and ensure compliance with relevant regulations. ISO 45001 promotes a proactive approach to risk management, encouraging organizations to identify and address potential hazards before they cause harm. This leads to a reduction in accidents, injuries, and illnesses, thereby protecting the well-being of employees and enhancing their morale. Achieving ISO 45001 certification demonstrates an organization’s commitment to safety and can enhance its reputation among stakeholders, customers, and employees. It also provides a competitive advantage by opening up opportunities for business growth, as many clients and partners now prioritize working with organizations that prioritize worker safety.
As per the International Labour Organization (ILO), the global toll of work-related accidents and illnesses is significant. Approximately 2.3 million individuals, both men and women, lose their lives annually due to work-related incidents or diseases, resulting in an alarming average of over 6,000 daily fatalities. Moreover, on a yearly basis, there are approximately 340 million occupational accidents and 160 million individuals affected by work-related illnesses worldwide. The ILO periodically updates these estimations, and the recent updates reveal a distressing rise in both accidents and occupational health issues.
– International Labour Organisation (ILO)
Quick Quote
Fill out the form below to find out more
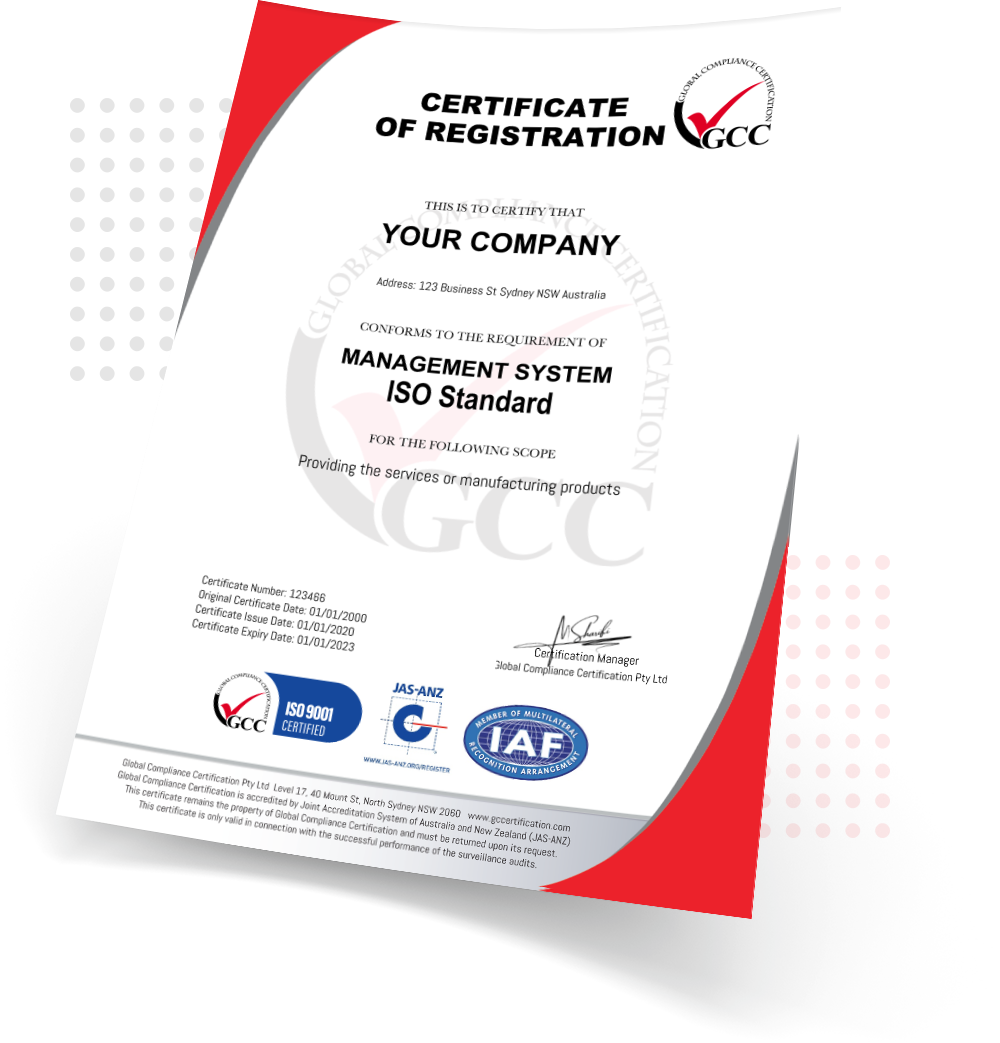
Focus of the ISO 45001
When an organisation implements ISO 45001, they are able to:
- Adopt one system across multiple sites and countries
- Align their processes with other standards that have been implemented
- Ensure all levels of personnel are actively participating in, and responsible for, a safe workplace
- Enhance their business credentials with certified evidence of their commitment to the safety of their employees
Benefits of ISO 45001
- Ensuring an organisational focus on legal & regulatory compliance
- Reduce injury and therefore the associated costs to the individual and the organisation
- Increase operational efficiencies due to decreased employee injuries and time-off
- Reduce insurance premiums (due to reduction in claims)
- Promote, internally and externally, the organisation’s commitment to a safe work environment
- Promote a system that is internationally recognised and benchmarked
Certification Process
Certification involves GCC assessing your organisation in order to ascertain that management systems meet the requirements of one or more recognised standards. Becoming certified to a nationally or internationally recognised standard is of great benefit to an organization. It improves overall performance, builds confidence within stakeholder groups and broadens the scope of new opportunity.
Application/ Contract
- Application for certification by client
- GCC will review and provide certification proposal
- Client accepts the agreement and return to GCC
- Audit dates will be booked
- GCC conducts Gap Analysis (optional)
Certification Audit/ Transfer
- Stage 1 Audit, The Audit team will assess documentation and readiness of management system for Stage 2 Audit
- Stage 2, Certification Audit, Audit team will assess implementation of system and will verify any issues outstanding from the Stage 1 Audit.
- Organisation will be recommended for Certification after review and positive decision by the independent GCC certification Authority,
- A Certificate will be issued
Maintaining certification
Surveillance Audits
Each issued certificate has a three-year life period. Upon certification, an audit program will be created for regular audits over the three-year period. These audits confirm company’s on-going compliance with specified requirements of the standard. At least one surveillance audit per year is required.
Read our policy for use of Certification Marks
Re-Certification
Re-Certification
The certification expires within 3 years and a re-certification Audit will be conducted prior to the expiry date to ensure that Management System is maintained.
Frequently Asked Questions
ISO 45001 is the internationally recognised standard for Occupational Health and Safety. It is intended to ensure that both your employees and any visitors you may receive are adequately protected from the risks present in your business premises. These risks will of course differ from one organisation to another — the potential for accidents in an industrial environment is normally greater than it is in an office environment. Nevertheless, ISO 45001 recognises the importance of occupational health and safety in all types of commercial environments and its goal is to ensure that all risks are effectively mitigated.
ISO 45001 has been developed to ensure management and employees at all levels actively participate in Occupational Health and Safety. This will ensure a safer workplace and reduce the risk to people’s safety. In fact, successfully managing health and safety risks not only prevents injury, ill health, and death, it supports businesses and communities as well. ISO 45001 uses a systems approach which supports companies to achieve this.
For an OHS system to be effective and efficient, everyone in the company must believe that he/she shares some responsibility and support for maintaining a safe environment. This includes employees all the way up to the top management and directors. Company-wide engagement is one of the key focuses of ISO 45001 standard. ISO 45001 also recognizes the value of worker consultation in the development of better OHS practices and emphasizes on employees actively participating in the development, planning, implementation, and continual improvement of the OHS systems.
ISO 45001 requires an ongoing assessment of risks and opportunities which use a risk-based framework similar to Plan-Do-Check-Act model. This model, if implemented effectively, can manage OHS risks and can significantly reduce/prevent accidents, health issues and lost time injuries.
In common with all ISO standards, there is a 10-clause format that covers all the requirements of ISO 45001 2018. The main requirement is to have an effective occupational health and safety system in place that uses a risk-based approach to anticipate and take proactive measures to mitigate all potential risks in the workplace. This system must state how OH&S standards apply to your organisation, including a definition of all internal and external factors that may have a bearing on the safety of personnel in your premises. It should also include details of the roles and responsibilities assigned to teams and individuals in your organisation specifically as they apply to OH&S in the workplace. Other areas covered by the standard include the planning, support, operational control, performance evaluation and potential for improvement of your OH&S system.
The amount of time it takes to become ISO 45001 certified will depend on a number of factors. The size and complexity of your organisation, the resources you are willing and able to dedicate to the achievement of this goal and the priority it is given will play a role in the time taken. With our expert certification services, it may take as little as 45 days to complete all the necessary steps but the total time could be longer if any complications are encountered. What we can tell you is that all such complications will be handled in the most efficient manner possible by our team, speeding up the process considerably. For details of how we can help please call whenever convenient. And for more information about our approach to ISO certification and training, see here.
In addition to the benefits listed above, ISO 45001 certification will prove to potential customers and business partners that your organisation takes the health and safety of its employees and visitors very seriously. More importantly, it will demonstrate that you have taken effective steps to protect your workforce from the risks to which they may be exposed.
Achieving ISO 45001 certification involves several key steps. Here’s an overview of the process:
- Familiarize yourself with the standard: Start by obtaining a copy of the ISO 45001 standard and understanding its requirements. This will help you identify the necessary changes and actions required to align your organization’s OH&S management system with the standard.
- Gap analysis: Conduct a thorough review of your existing OH&S management system to identify any gaps or areas that do not comply with ISO 45001 requirements. This analysis will help you understand the scope of work needed to meet the standard’s criteria.
- Establish objectives and develop a plan: Set clear objectives for achieving ISO 45001 certification, including timelines and responsibilities. Develop a detailed plan that outlines the steps, resources, and activities required to meet these objectives.
- Policy development: Develop an OH&S policy that aligns with ISO 45001 principles and reflects your organization’s commitment to worker safety. Ensure the policy addresses key elements, such as hazard identification, risk assessment, and employee participation.
- Implementation: Implement the necessary changes and improvements to your OH&S management system based on the identified gaps. This may involve updating procedures, providing training to employees, and establishing new processes to address specific requirements of the standard.
- Documentation: Create the necessary documentation to support your OH&S management system, including policies, procedures, work instructions, and records. Ensure these documents are readily available, easily accessible, and up to date.
- Internal audit: Conduct an internal audit of your OH&S management system to assess its effectiveness and identify any non-conformities. This step helps you identify areas for improvement and ensure compliance with ISO 45001 requirements.
- Management review: Hold a management review meeting to evaluate the performance of your OH&S management system. This review should include a discussion of audit findings, corrective actions, and opportunities for improvement.
- Certification audit: Engage an accredited certification body to conduct an external audit of your OH&S management system. The certification body will assess your compliance with ISO 45001 requirements and determine if you meet the criteria for certification.
- Corrective actions: Address any non-conformities or observations identified during the certification audit. Implement appropriate corrective actions to resolve any issues and ensure compliance with ISO 45001.
- Certification: If your organization successfully meets all the requirements of ISO 45001, the certification body will issue an ISO 45001 certificate. This certification demonstrates your organization’s commitment to worker safety and adherence to internationally recognized OH&S standards.
- Continuous improvement: ISO 45001 certification is not a one-time achievement. Maintain and continually improve your OH&S management system by conducting regular internal audits, monitoring performance indicators, reviewing and updating policies and procedures, and engaging employees in ongoing improvement initiatives.
By following these steps, organizations can work towards achieving ISO 45001 certification and establish a robust occupational health and safety management system.
GCC Training
Empower your team with our self-paced efficient training.